





Share to
YKW Series of High Speed Flexo lnk Corrugated Paperboard Printing Sloting Die Cuting Machine
Still deciding? Get samples first, Contact US !
View similar products
Tag list
Product Feature:
1.All the main electric appliances of the whole machine adopt the product of Schneider made in France.
2.Adopt lead-edge feeder system.(optional servo feed system)
3.Aiitpiv-he gears are made from high frequency.
4.All axles of roller must be chrome-plating in order to increase the hardness.
5.The gears adopt shower type circular lubricating with oil balance
6.This machine adopts PLC &touching screen.Muli functional control,and frequency conversion control machine which are precise and reliable.
7.Automatically changes back to zero and correct the plate making.
8.Adopting the mould piece designing.The multi-color printing machines can be combined and linked in anyway.
9.Flexo plate rol ler lateral adjustmenta dopt computer PLC contol.
10.Cutter mould rol ler and soft roller a do pt international standard size. with easy purchasing mould and cushion.
11.With compensating device to follow and compensate the speed of cushion roller,making sure that the sizes of the box and the cutte mould are the same.
Product parameters:
Serial | Name of parameter | Unit | Specification | |
YKW920 | YKW24 | |||
1 | Width of inside machine | mm | 2400 | 2800 |
2 | Design speed | pieces/min | 450 | 400 |
3 | Maximum size of feeding paper | mm | 900×2000 | 900×2400 |
4 | Minimum size of feeding paper | mm | 280×600 | 280×600 |
5 | Feeding paper by partition | mm | 1100×2000 | 1100×2400 |
6 | Maximum printing area | mm | 900×1960 | 900×2360 |
7 | Precision of process printing(Double/three/four color) | mm | ±0.5 | ±0.5 |
8 | Thicknessof standard printing plank | mm | 7 | 7 |
9 | Thickness of printing paperboard | mm | 2-11 | 2-11 |
10 | Minimum slotting space (same knife direction) | mm | 230×60×230×60 | 230×60×230×60 |
11 | Maximum slotting depth | mm | 225 | 225 |
12 | Printing roller axle-oriented regulating | mm | ±10 | ±10 |
13 | Maximum die-cut size | mm | 850×1950 | 8150×2350 |
14 | Die-cut thickness | mm | 2-8 | 2-8 |
Product information:
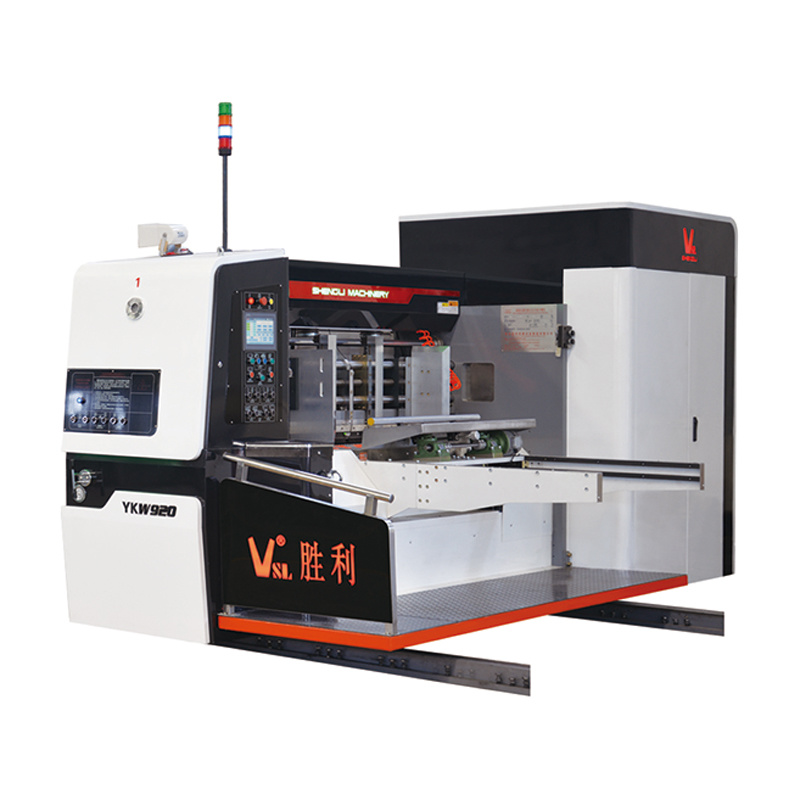
Function of Feeding Department
1.Feeding unit adopt mechanical lead edge feeding system.
2. Three shaft lead edge feeding. smooth and accurate
3. Assistant suction(7.5KW), wind energy and press be controlled by transducer thereby adapt differ paper inguiry.
4. Front baffie clearance adjusting adopt protruding wheel configuration also convenience and apply.
5. Provide paper glue roler adopt elasicdly and foac out. Not ony ensure provide veracly but also avoid press bad cardboard.Adust capaclybe conroled by elecic machinery and
showing nicety and trustiness by touch screen.
6. The up and down of the back baffle movement and front and back movement all controlled by the compressed airmotor, convenient and swift.
7. Eleclric control machine separation and reunion together with alarm bell it will persist beling when traveling. Then insure safety of operator.
Function of Printing Department
1. Can adopt the single doctor blade The system can ensure that the ink rollernetwork points transferred to the plate, and can completely control the amountof ink in the ink, ink stability. To print finer lines, high DPl, print cardboard better.easy maintenance.
2. All roller adopt super steel. Adjust by transfer balance and made by platingchrome and skiving.
3. Printing phasic adopt PLC touch screen control and electric data 360adjust(when dynamic and static state should adjust.)
4. Roller transverse adopt electric control and transverse adjust distance is 20MMIt can should auto refer middle.
5. lt has oil base ink monitor and control stop provide paper after alarm without oibase ink.
6. Load and unioad space of printing. foot step switch control positive andnegative turning.
7. The gap of the adjustment of the transfer roll impressing roll rubber roll and theanilox roll adopt squagging instruction.
8. The feeding wheel adopt swift movement instruction . made the adjustmenteven swift and convenice .
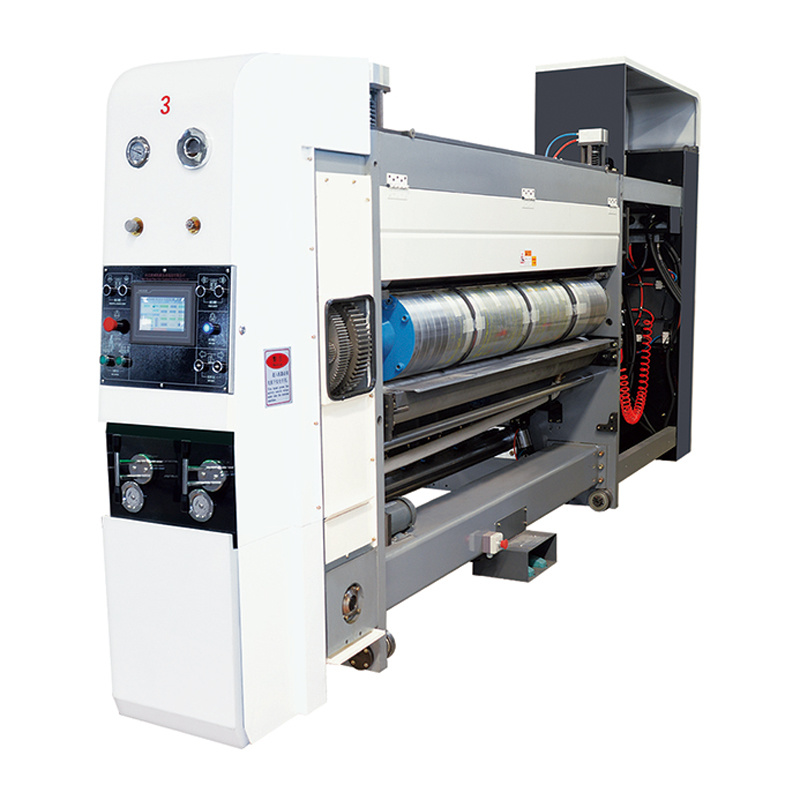
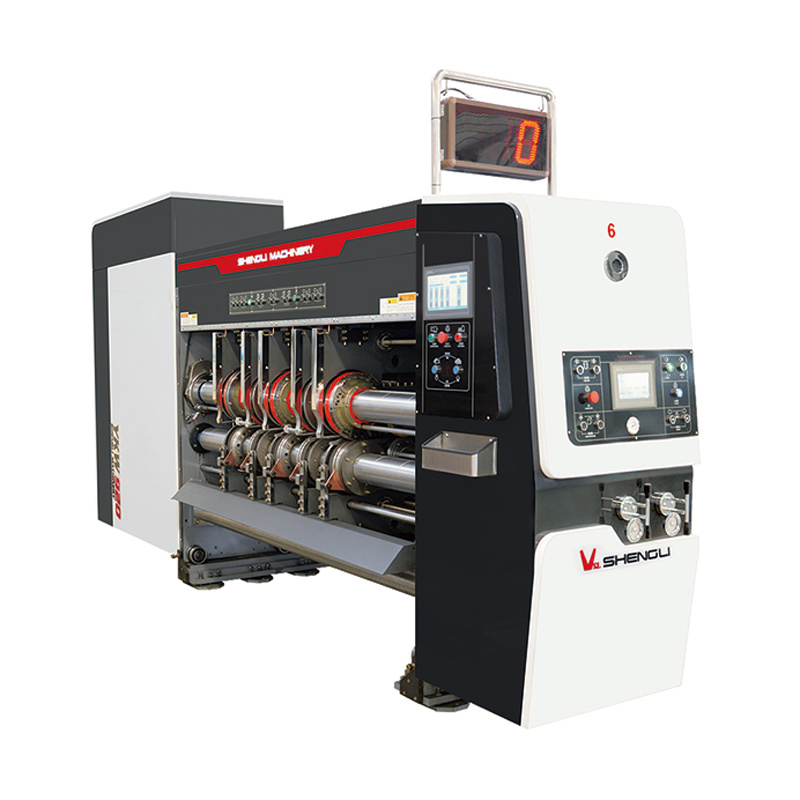
Function of Slotting Department
1. lt adopt single shaft double knife slotting, pre-creasing then creasing, the pressing effection evenbetter. it's good for the producing processing after gluing box follow-on equipment.
2.Upper pressing wheel wrap rubber spring outside, don's damage the paperboard.
3. The gap of the pre-creasing wheel, creasing wheel and the slotting knife adopt squagging instruction.
4. Transfer of notch knife seat adopt ball bearing silk bar and long life and high nicety.
5. The pressing wheel, slotting knife seat sway adiustment at the same step. the PLC adjusting.
6. Notch knife width 8.0 MM, it adopt alloy steel material. After heat treatment and grinding, bladetartness and long using life.
Function of Rotary Die Cutting Department
1. Die-cut phase and the gap between the cutter mould rollers are both controlled by computer.
which can display but aslo can to set up.
2.The cushion roller adopts mechanical camdrum portable structure (40mm).
3. The gap between the cushion roller and the cutter mould roller adopts electrical adjustmentWhen stopping feeding paper. the soft will rise automatically; When working, the soft roller willreturn to the working position.
4. Adopt compentating system, No matter how much the cushion diameter changes. The speed ofthe cushion compentate and follow automatically, without adiustment by man.
5. With restoration for cushion after wear and tear, Keeping the surface of the cushion smooth.
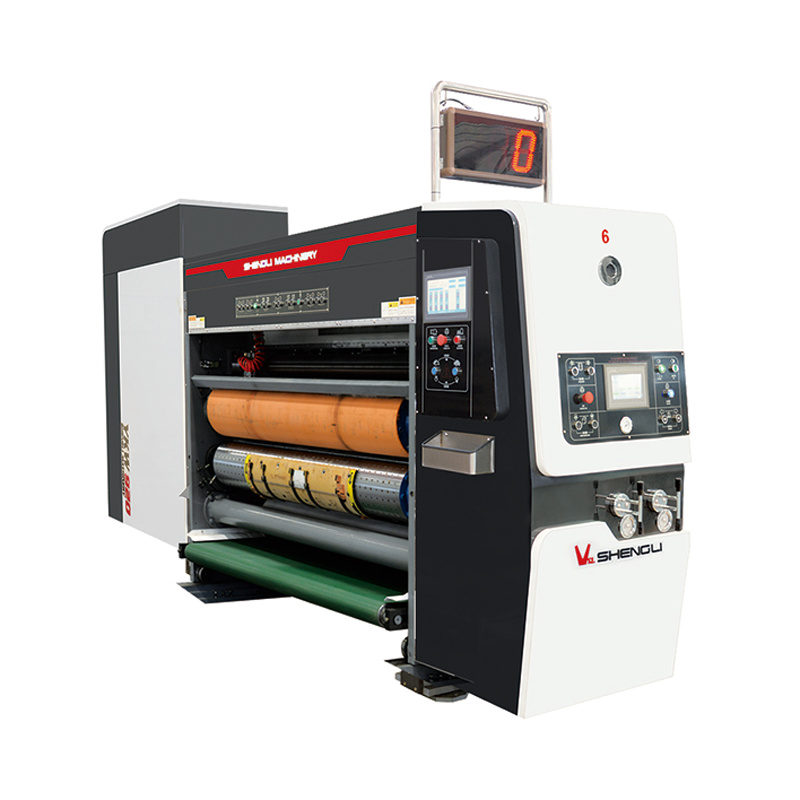
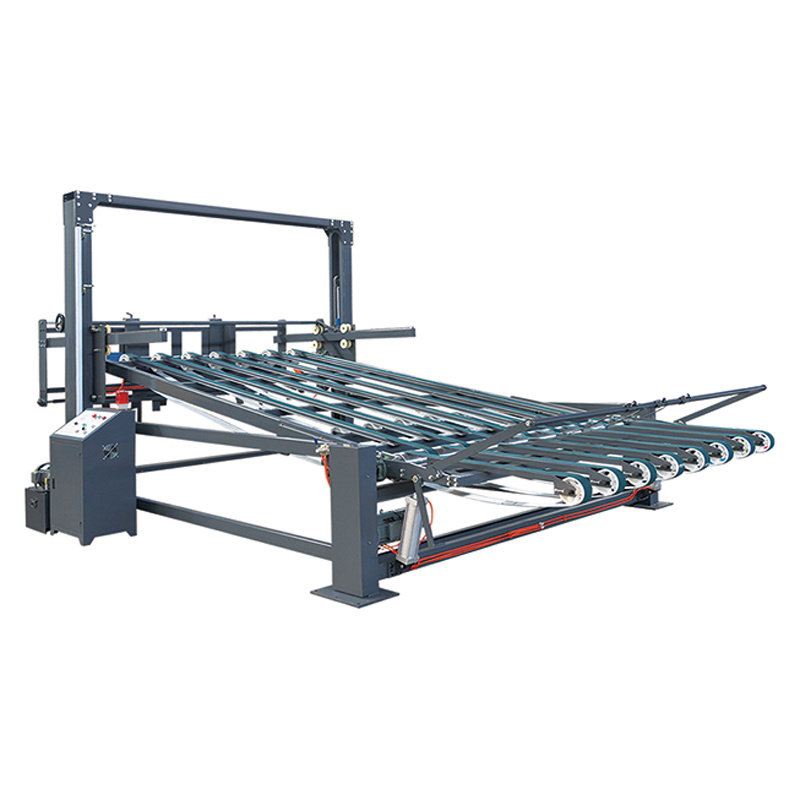
Hydraulic Stacker
1.Bin arm using pneumatic operation, manual control.
2.Bedtable lifting, hydraulic station double hydraulic cylinder drive, to ensurethe safety of operators.
3.Stacking, using a flat wrinkles climbing belt and steel clamping device, sothat the stacking order and tidy.
4.Hold paper feeder can be adjusted to hold the opening width, with a batch accumulation function.
5.The use of side shoot baffles to ensure more orderly stacked cardboard.
6.Electric enforce the use of PLC programming control, independent of the operating electric box.
7.Optional vibration stripping and lateral waste function.
8.Stacker height: 1600mm.
Finished Product:
Our Advantages:
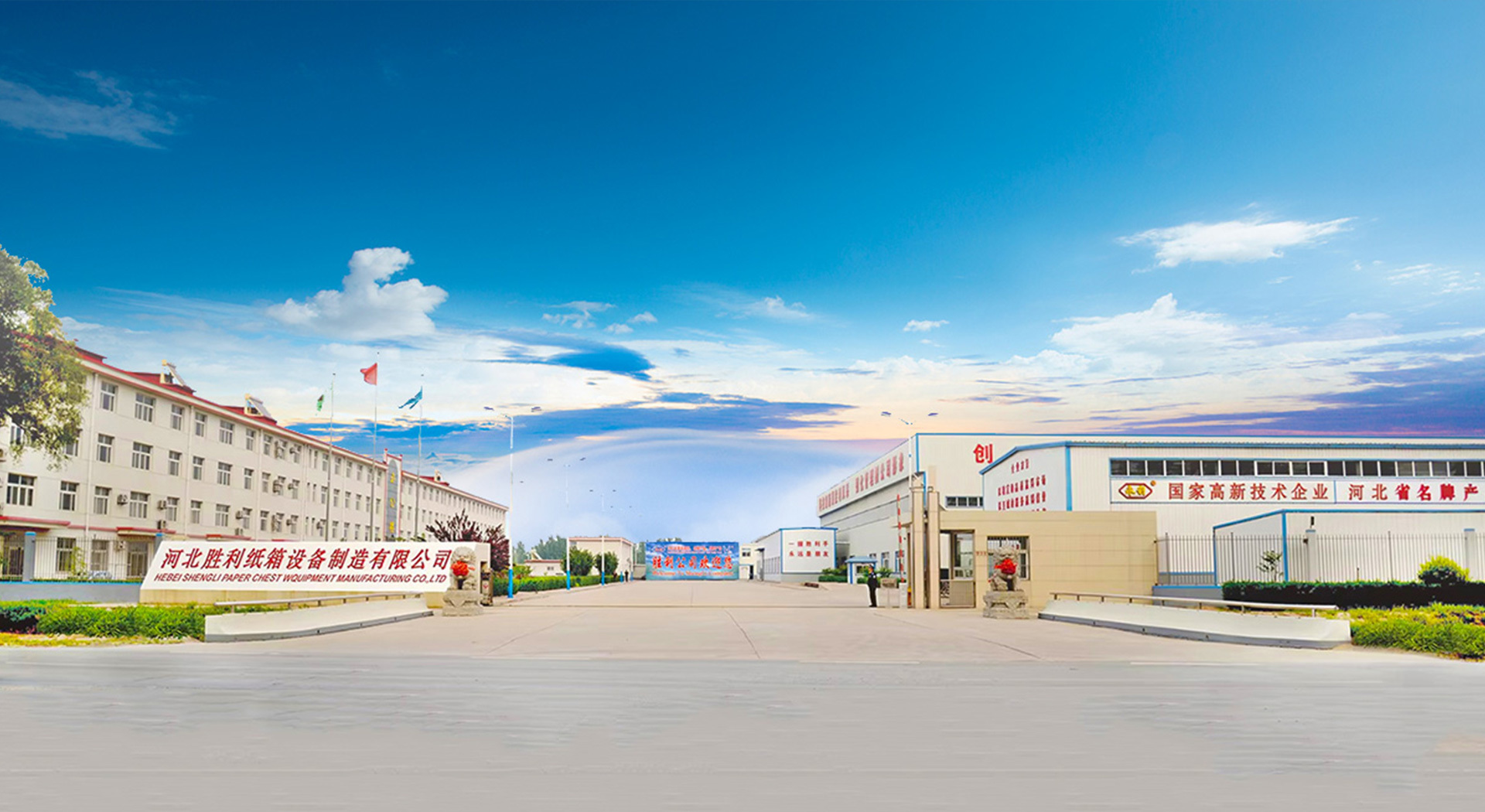
Professional cardboard box machinery manufacturer
Our main units include pressure corner slicers, slitting machines, 3, 5 and 7-ply corrugated cardboard production lines, automatic and chained rotary die-cutters and rolling lines, single face corrugated cardboard machines, paper rolling lines, pasting machines, platform grinder slicers, stitching machines and other related products.
■ Superior geographical location
■ Advanced equipment and excellent product quality
■ Our products are exported overseas
Company exhibition:
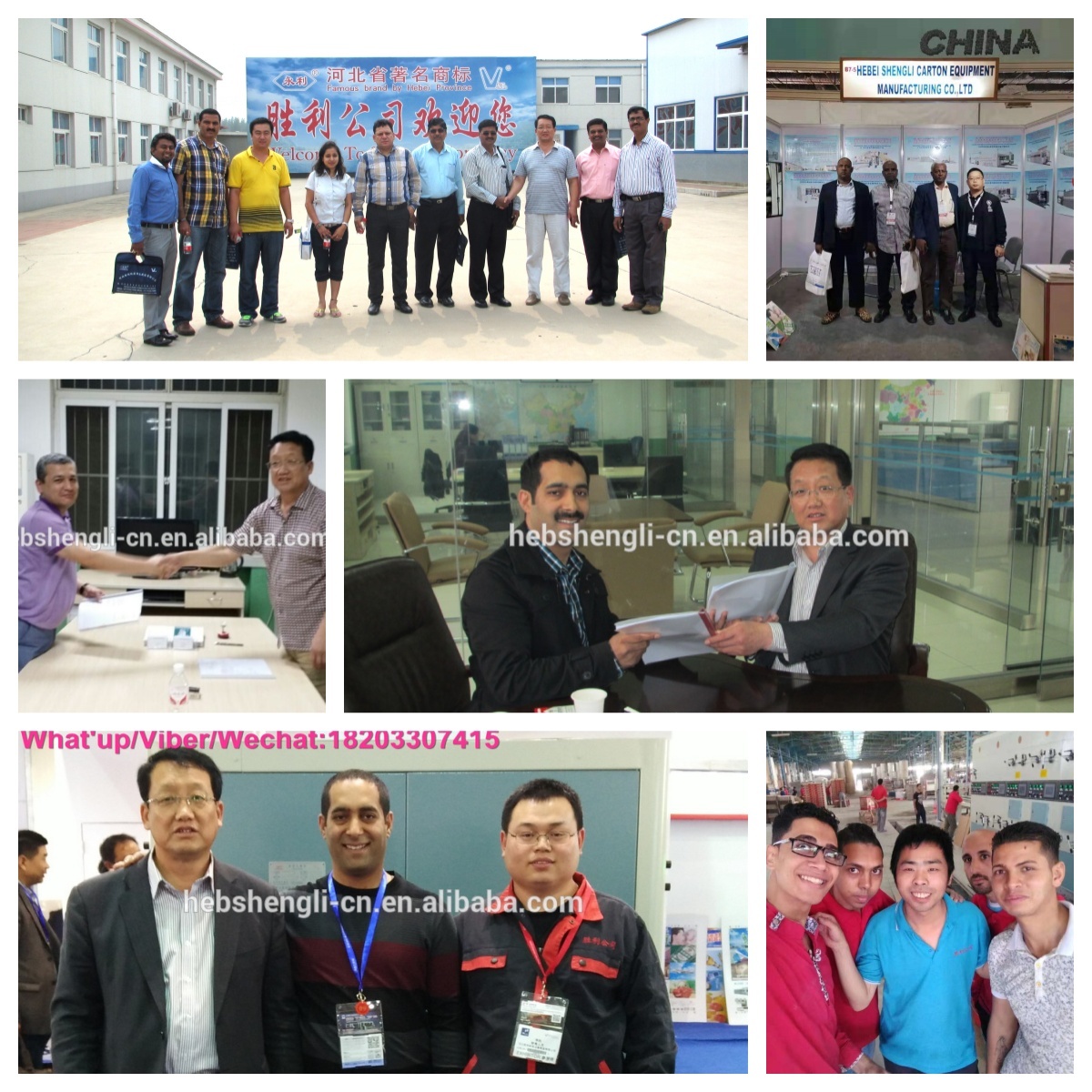
QUALIFICATION:
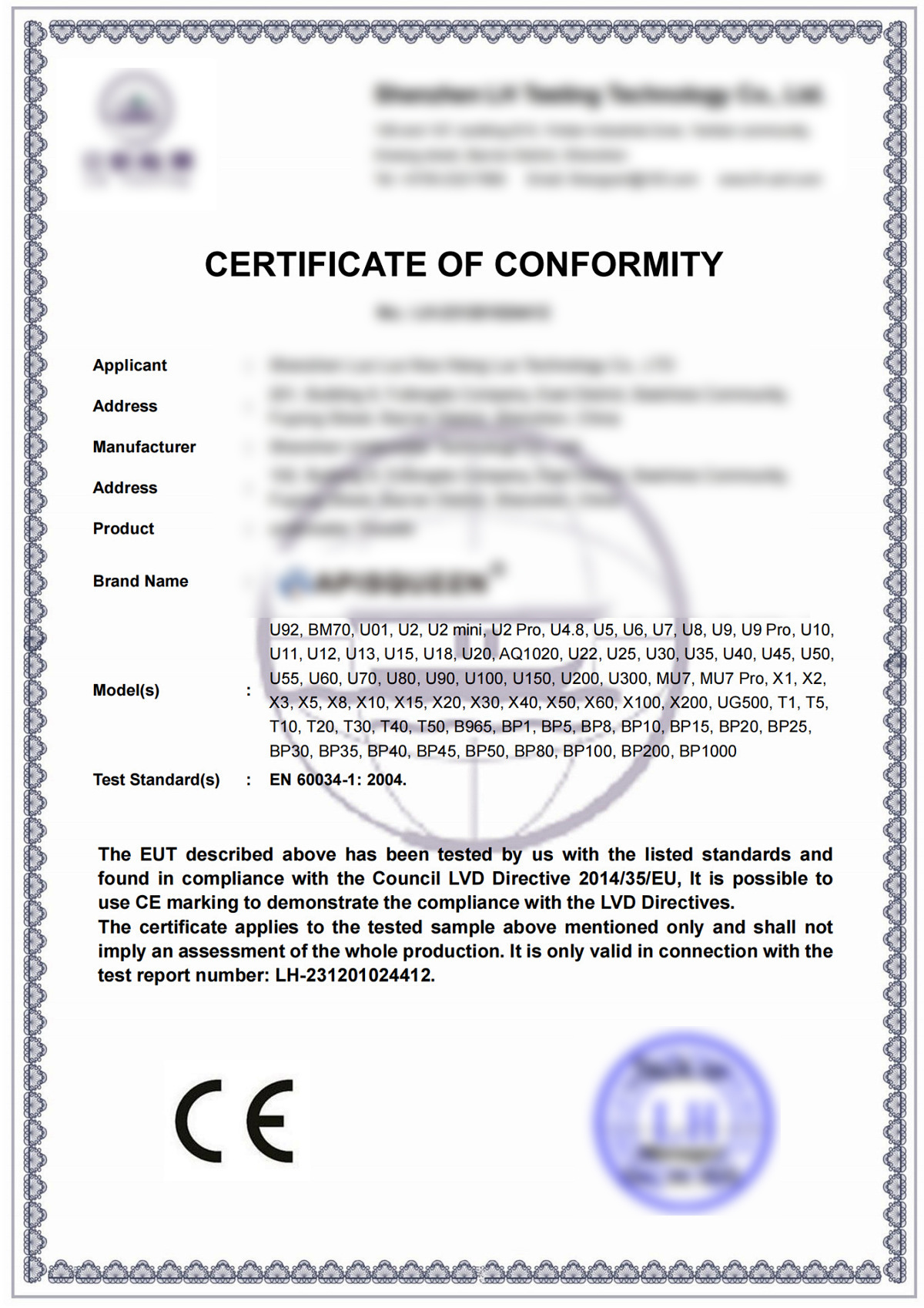
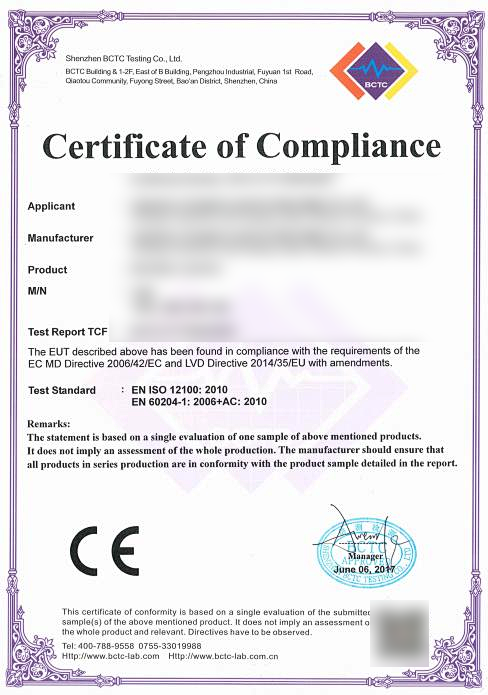
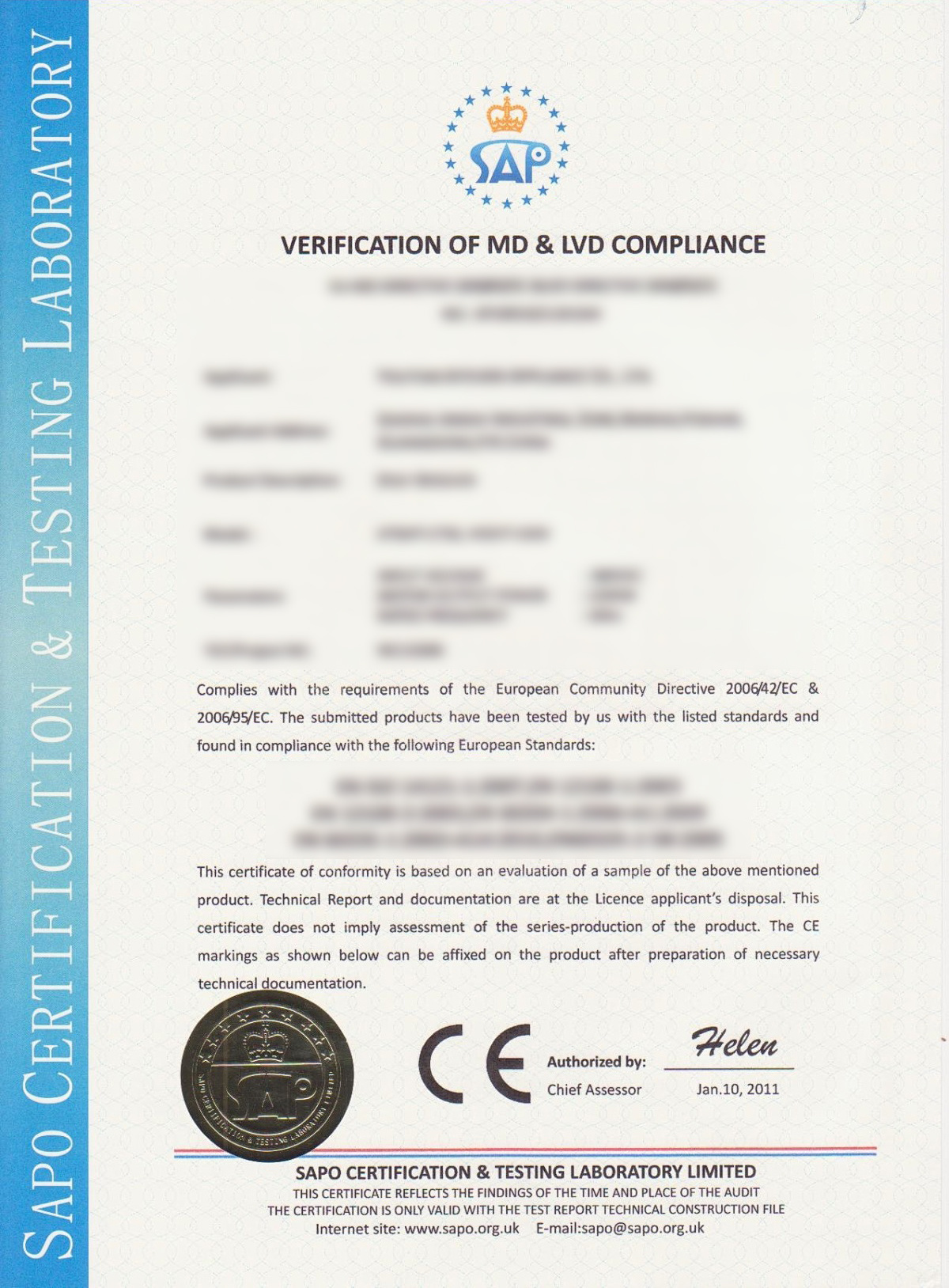
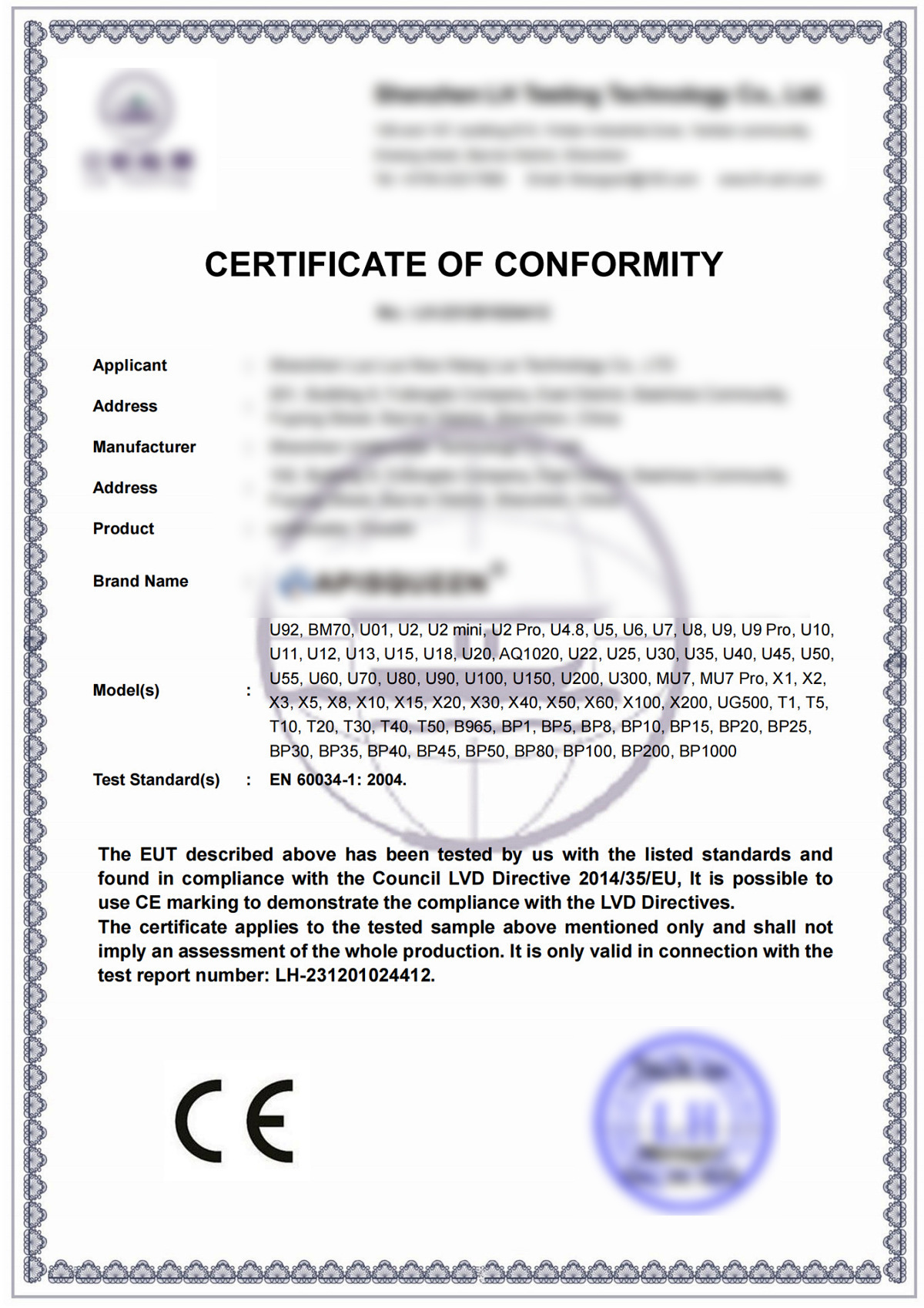
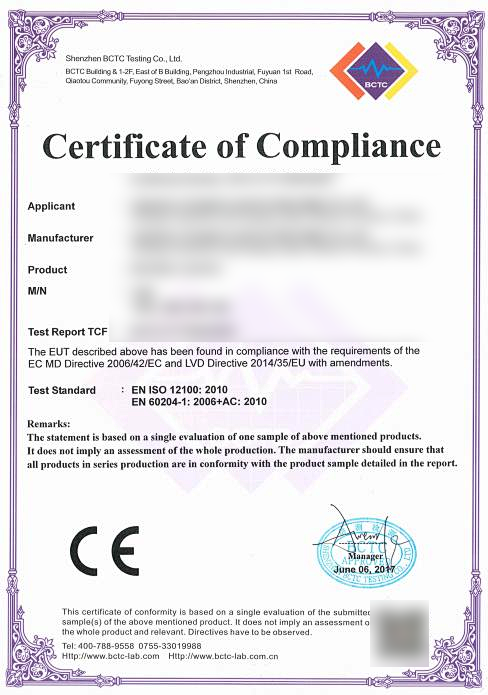
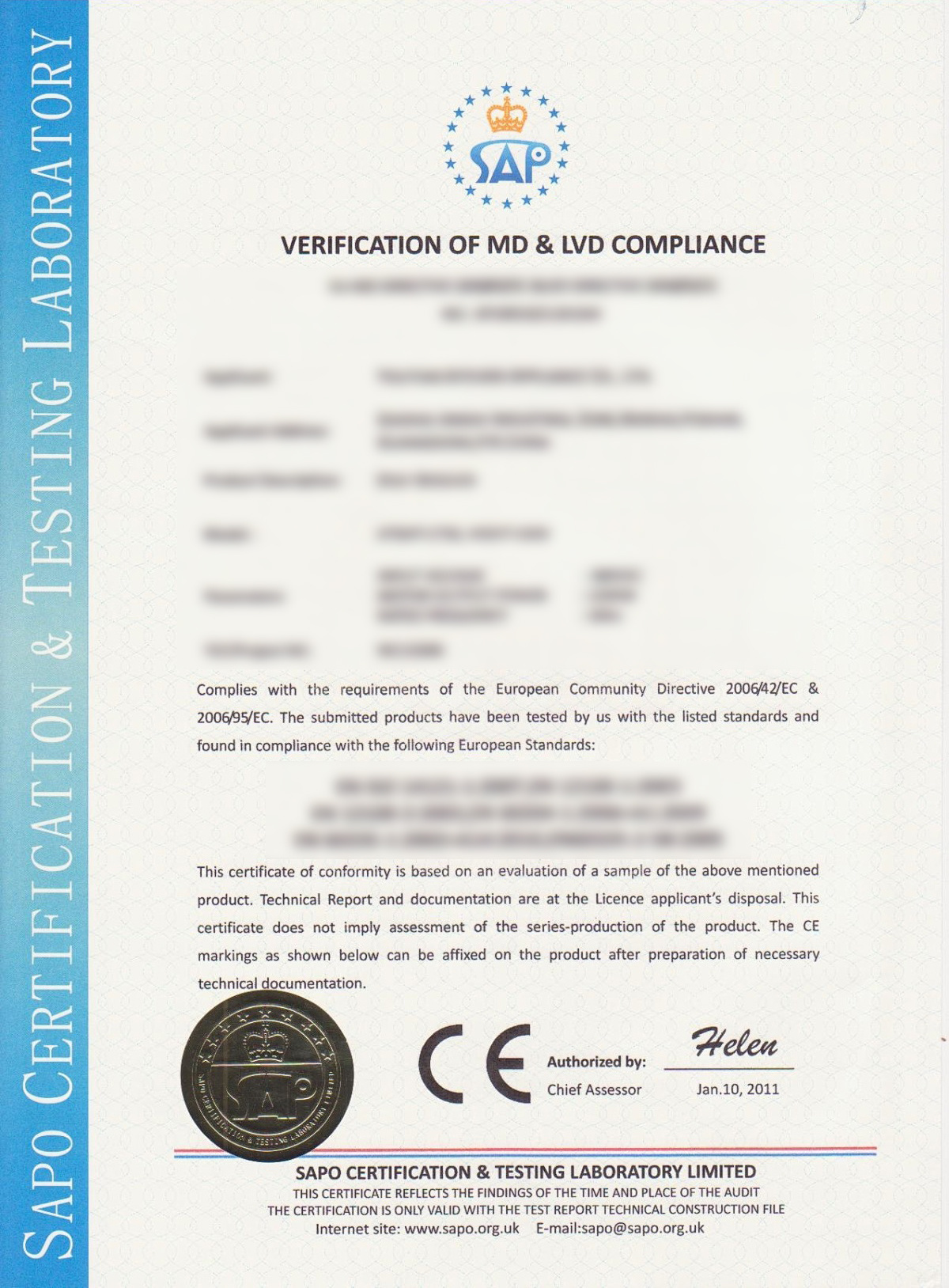
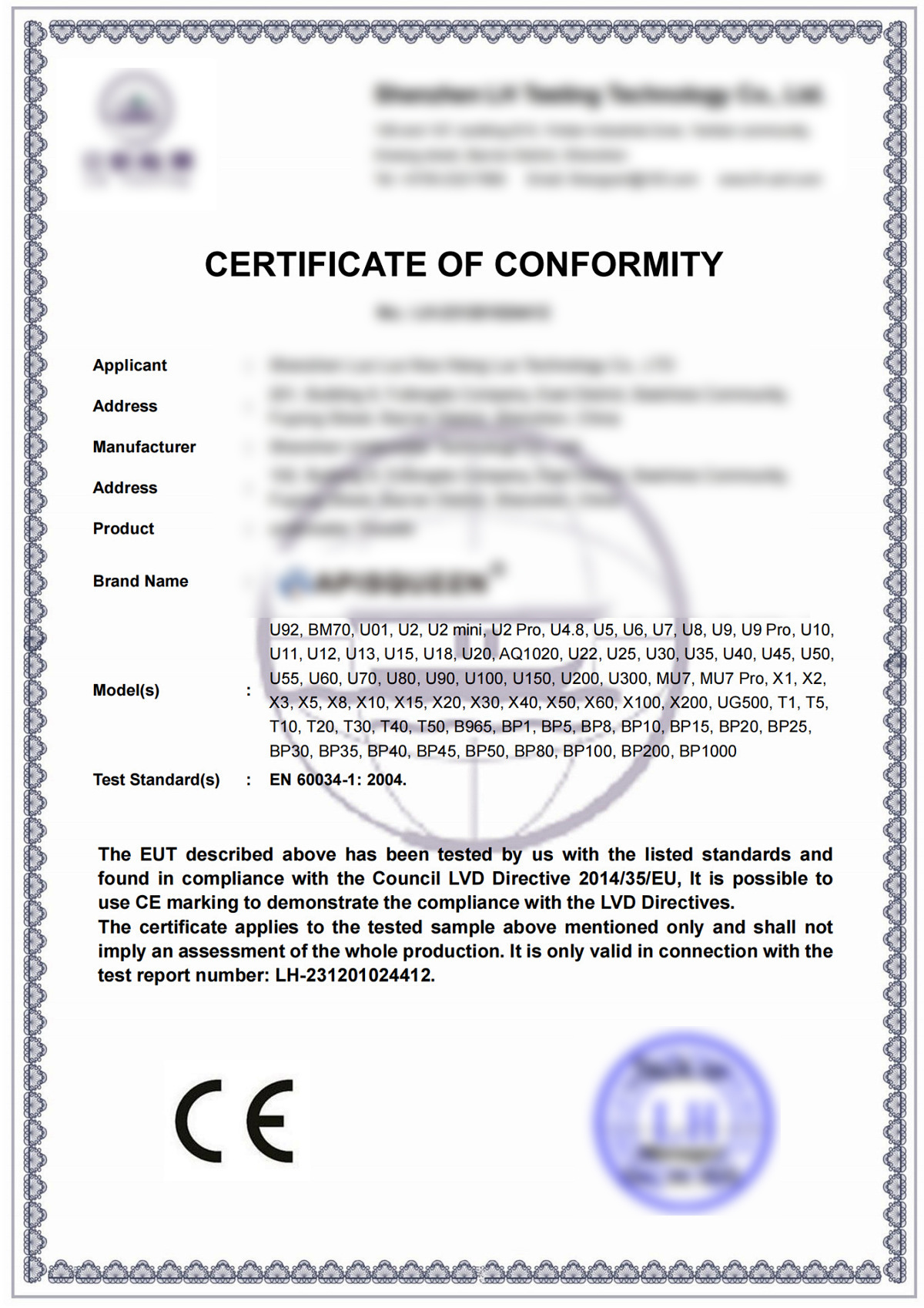
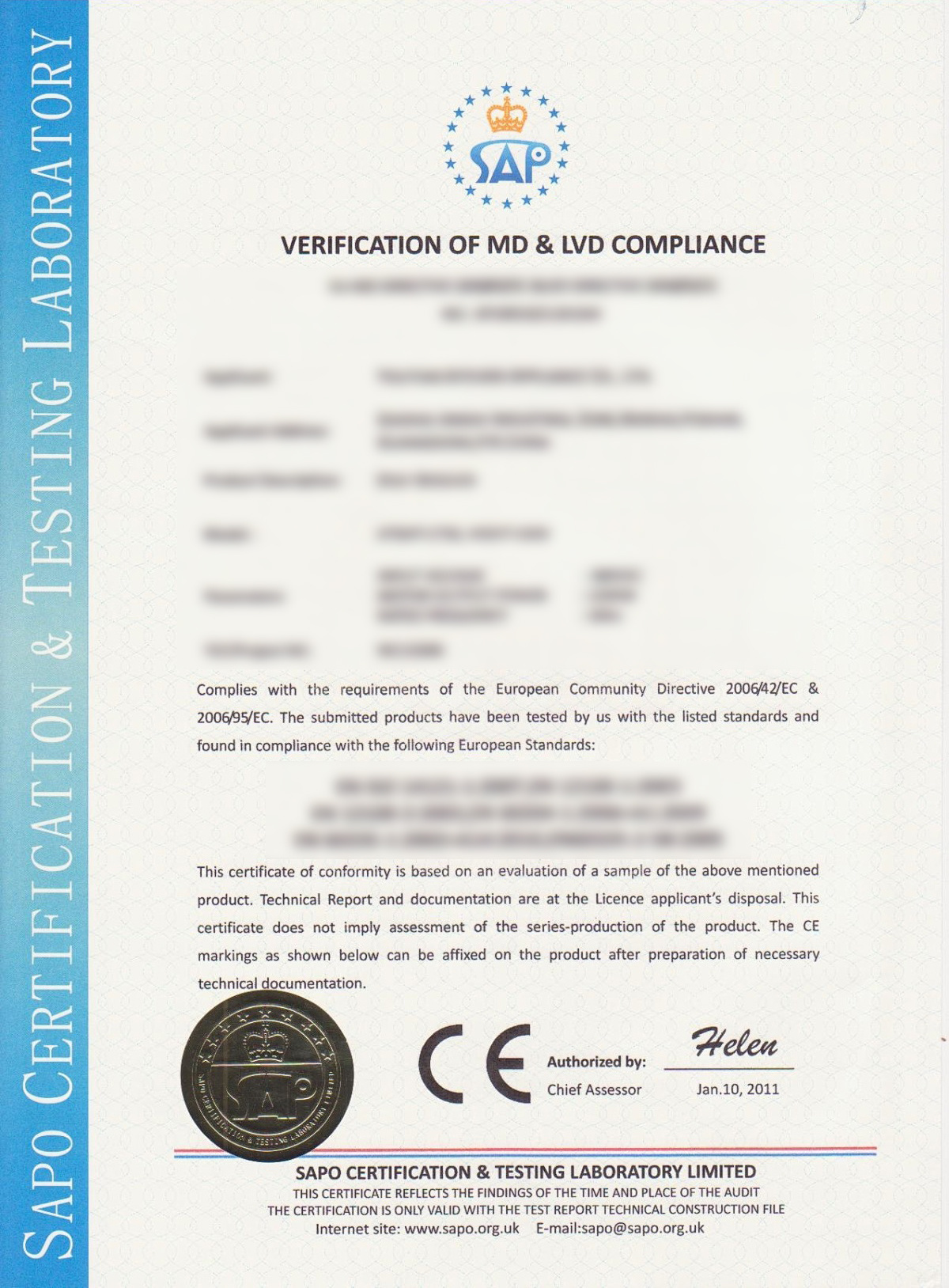
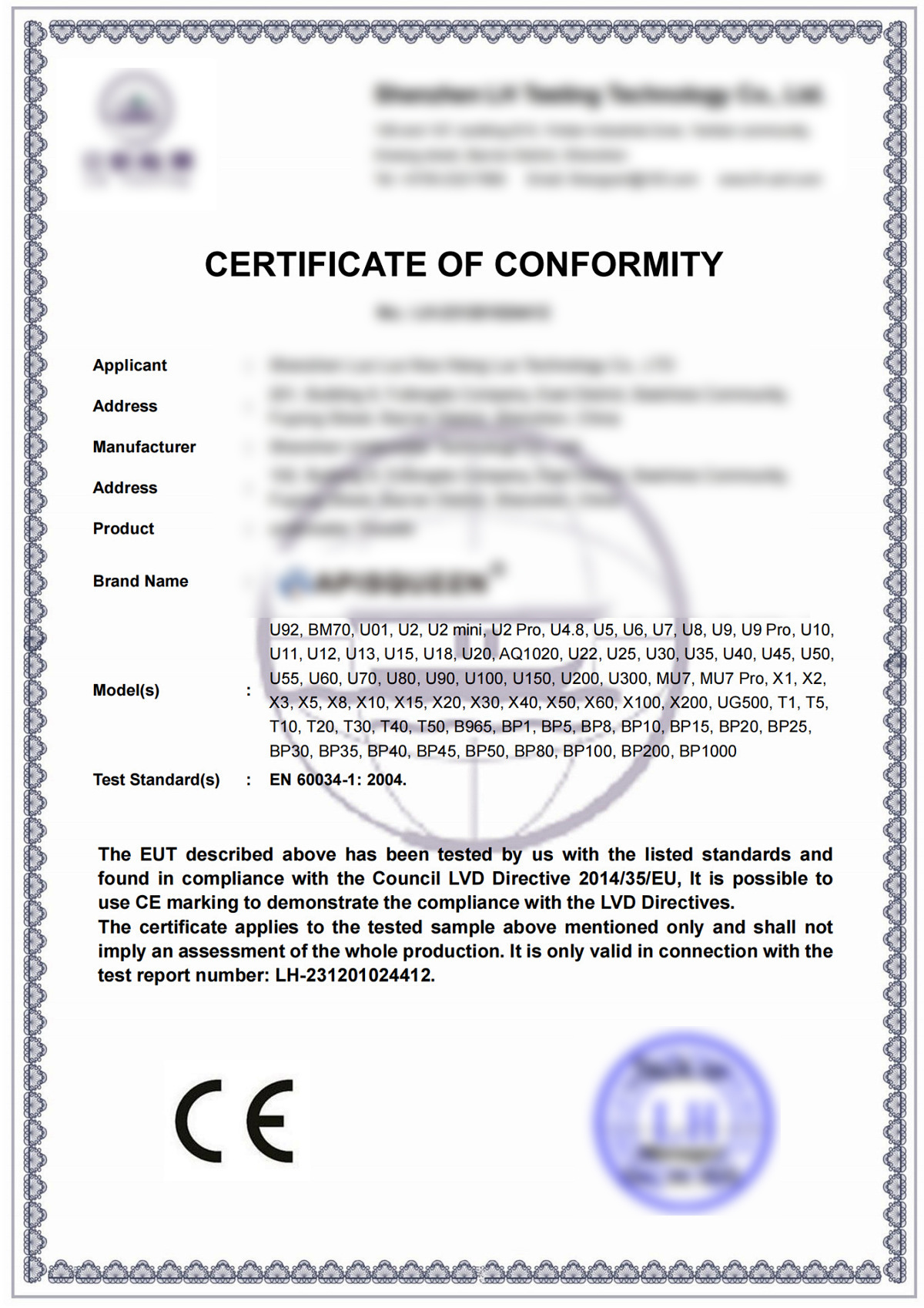
YKW Series of High Speed Flexo lnk Corrugated Paperboard Printing Sloting Die Cuting Machine
Still deciding? Get samples first, Contact US !
Products Category
Keywords
Related Products
Inquire Now
If you are interested in our products, please leave your email and we will contact you as soon as possible. Thank you!